Assure manufacturing excellence through robust process validation methodologies. From installation to performance, we provide end-to-end guidance.
Injection Molding Process Validation for Quality Assurance and Regulatory Compliance
At Suensa, we offer comprehensive injection molding process validation services built on a foundation of industry standards, regulatory expectations, and scientific molding best practices. Our validation framework, covering Installation Qualification (IQ), Operational Qualification (OQ), and Performance Qualification (PQ), ensures that your injection molding processes are not only optimized but fully validated to produce consistent, compliant, and high-quality parts.
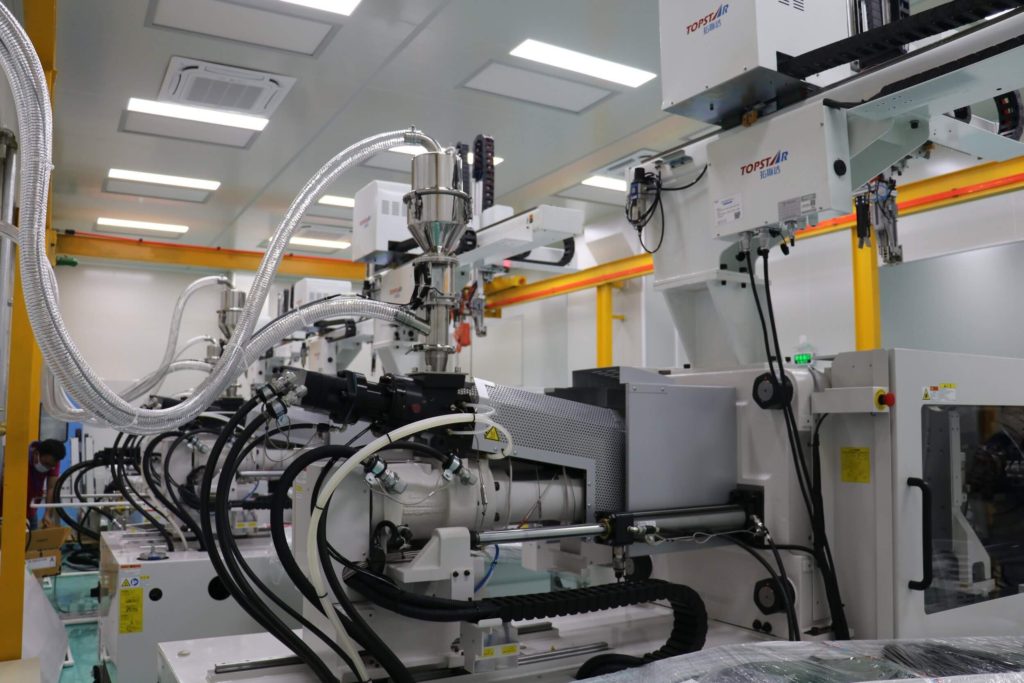
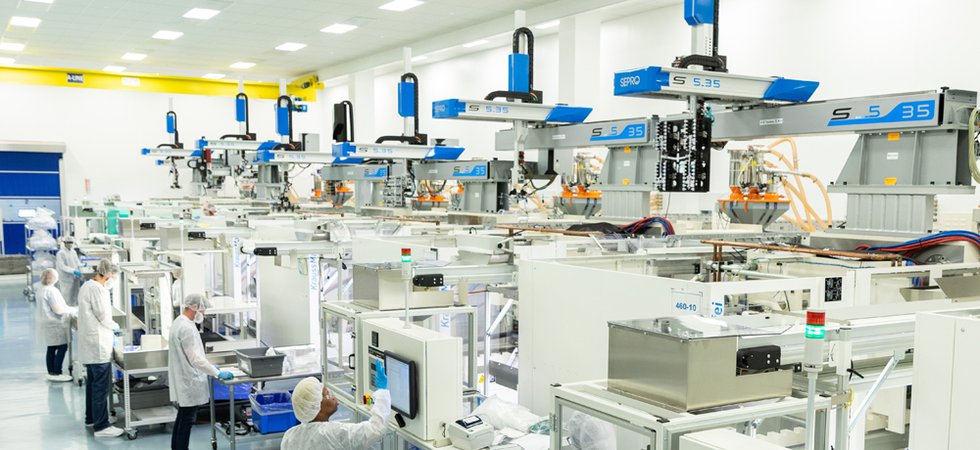
Injection molding is a complex and intricate process that demands precision, expertise, and a deep understanding of material behavior and machine dynamics. Process validation is critical in regulated industries such as medical, automotive, and aerospace manufacturing, where product consistency and traceability are non-negotiable. Whether launching a new mold, changing materials, transferring tools, or introducing new equipment, our process validation services ensure that your operations meet specifications and stay compliant with ISO, FDA, and GMP requirements.
Key Focus Areas
- Validation Master Plan (VMP)
- IQ, OQ, PQ protocols and execution reports
- Equipment calibration certificates
- Gage R&R studies and capability analysis
- Statistical Process Control (SPC) studies
- Process Flow Diagrams (PFD), PFMEA, and Control Plans
- Design of Experiments (DOE)
- Part inspection results and dimensional reports
- Approved setup sheets and baseline parameters
- Cleanroom protocol compliance
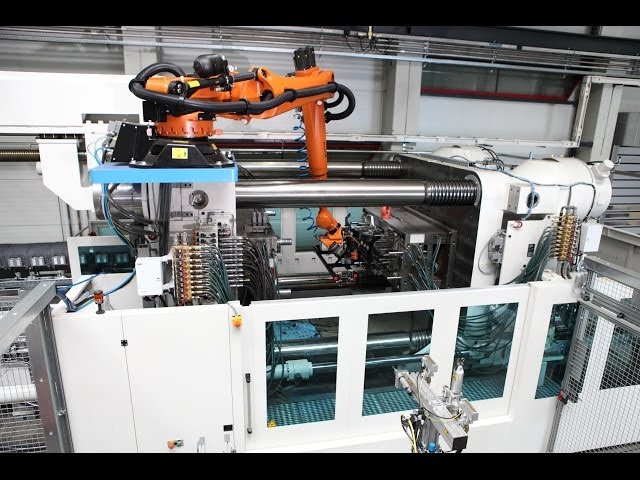
Our Three-Phase Validation Framework
1. Installation Qualification (IQ)
We begin by verifying that all equipment and systems are installed correctly and conform to manufacturer specifications and facility requirements. Our IQ documentation includes:
- Equipment verification (IMM, molds, auxiliary systems)
- Utility connection verification (electrical, hydraulic, pneumatic, and water)
- Mold installation and leveling
- Calibration checks of temperature controllers, pressure sensors, and timers
- Verification of environmental conditions (cleanroom, HVAC, etc.)
- Equipment manuals and validation protocols
- All findings are documented with traceable records to establish a compliant installation baseline.
2. Operational Qualification (OQ)
Next, we validate that the equipment and system operate consistently within defined parameters. This involves:
- Process parameter testing across upper, nominal, and lower limits
- Statistical testing (DOE, SPC) to establish operating ranges
- Equipment functionality checks (clamping, injection, ejectors, robot EOAT, etc.)
- Safety system verification
- Alarm and interlock testing
- Control system validation and data integrity verification
- The OQ phase confirms that the process controls and tolerances are capable of stable and repeatable operation.
3. Performance Qualification (PQ)
In the final phase, we validate the process under actual production conditions using approved materials and trained operators:
- Production of consecutive shots at nominal settings (typically 3–5 runs)
- Detailed dimensional and visual inspection of parts
- Cavity balance verification and pressure consistency
- SPC analysis to ensure outputs fall within process capability (Cpk/Ppk thresholds)
- Packaging and labeling verification if applicable
Upon successful PQ, the process is released for routine production, with validation protocols and batch records available for audits or regulatory review.
Why Process Validation Matters
Ensures consistent part quality
Process validation confirms that critical process parameters are capable of producing parts within defined tolerances. This consistency minimizes rework, scrap, and customer complaints over the lifecycle of the mold.
Reduces risk of process variability or non-conformances
By thoroughly testing process windows and equipment functionality, validation identifies potential sources of variation before they impact production. This proactive approach strengthens your quality control system.
Meet regulatory requirements (ISO 13485)
Regulatory agencies and industry standards require documented evidence of process capability and control. Our validation protocols align with these frameworks to ensure compliance and audit readiness.
Accelerates production ramp-up with proven stability
Validated processes shorten the path from development to full-scale manufacturing by removing uncertainty. With known capability, your team can move forward with confidence during launch phases.
Builds confidence in new or transferred tooling
Whether introducing a new mold or relocating a validated tool, IQ/OQ/PQ establishes that it performs as intended in its current environment. This reduces startup risk and supports reliable production outcomes.
Supports continuous improvement and traceability
Process validation creates a data-driven baseline that helps monitor long-term performance. This foundation allows for informed adjustments, better root cause analysis, and continuous improvement over time.
process validation
Pricing
Process Validation
Starting From,
$3499
per process
- Full IQ, OQ, PQ execution
- Validation documentation package
- In-plant(*) or remote support
- Setup sheet and part approval report
- Cpk/Ppk and SPC charts
- Become Audit-ready
- Process Optimization
- Continous Process Improvements
- Process Troubleshooting
* In-plant support may be subject to additional charges like hourly rate or travel expenses.
Partner with Suensa for Reliable Validation!
Get Started Today!
Whether you’re validating a single mold or an entire production cell, Suensa’s experienced consultants provide the guidance and documentation necessary for robust, compliant process validation. We blend scientific molding, Six Sigma, and regulatory expertise to validate your processes with confidence.
Contact us today to learn how our Process Validation services can support your next launch or audit preparation.
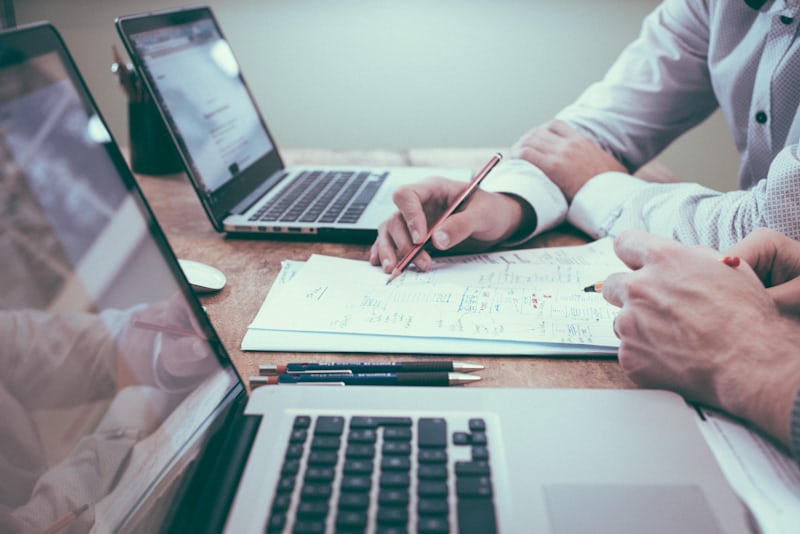